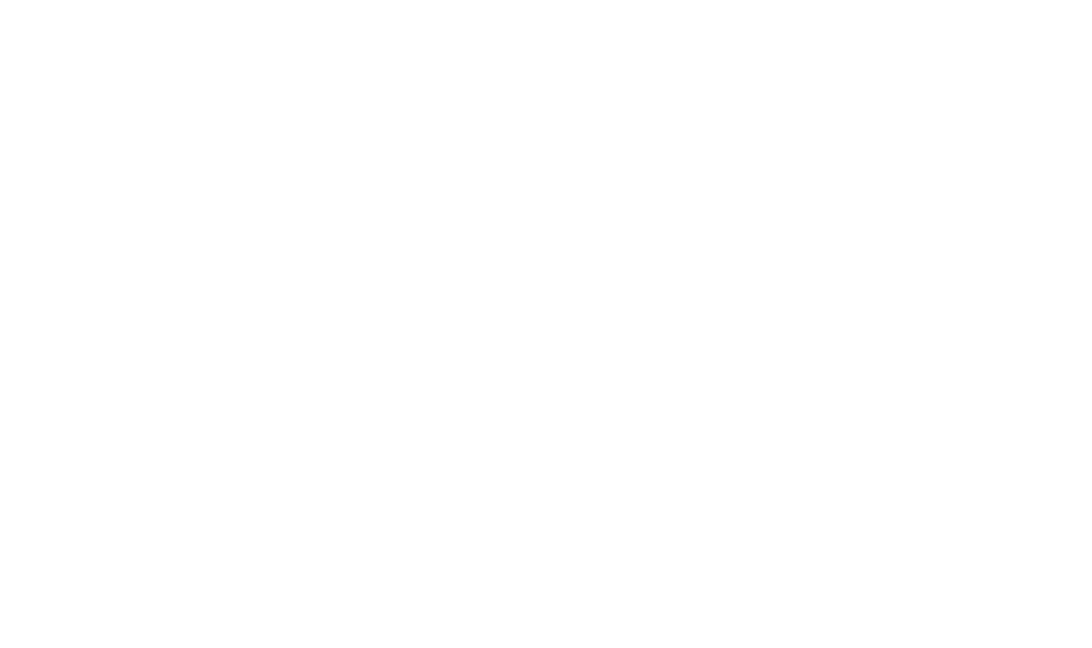
Menu
The UNLOCK project is dedicated to developing environmentally friendly solutions by transforming poultry feathers into sustainable bioplastics. This innovative approach uses feather keratin to create sustainable and biodegradable materials (bioplastics) that then will be used to produce agricultural products, including forest and seed trays, mulch films, non-woven geotextiles and hydroponic foams. These bioplastics are designed to naturally break down, reducing environmental impact and contributing to a more sustainable agricultural ecosystem.
CIDETEC, coordinating the UNLOCK project, plays a pivotal role in the development and application of these bioplastics. In this interview, Sarah Montes, the project coordinator from CIDETEC, discusses the UNLOCK project's innovative approach to converting poultry feathers into biodegradable bioplastics for agricultural use. She addresses the technical and environmental challenges of the production process, the properties of the materials, and their practical applications in agriculture.
1. Material Selection Process
Q: How are biodegradable polymers and feather keratin selected for the bioplastics development in UNLOCK?
A: Biodegradable polymers have been selected based on their intended application: forest and seed trays, mulch films, non-woven geotextiles and hydroponic foams. Depending on the requirements of each application, the processing requirements and mechanical properties of the materials have been assessed, as well as the desired end of life. At UNLOCK we have an industrial compounder BIOMI specialised in the development of biodegradable compounds. Based on BIOMI's know-how in this field, tailor-made compounds have been developed for UNLOCK.
2. Material Qualities
Q: What qualities do you look for in both the biodegradable polymers and feather keratin to ensure that these materials are working well together and are environmentally friendly?
A: The main criterium is the intended end of life of the product for each application. Depending on this matter, we selected the suitable blend of polymers. What we have observed is that in general, the incorporation of feathers improves the biodegradation behavior of materials. Moreover, the addition of feathers increases the biobased content of the product.
3. Compounding Process
Q: Can you describe the process of mixing feather keratin with biodegradable polymers to create keratin-based bioplastics? What are the critical conditions needed for effective blending?
A: One of the advantages of the UNLOCK developments is that conventional, well-established and well-known polymer processing techniques such as extrusion can be used. In the particular case of the mixing of feathers with biodegradable polymers, special attention must be paid to temperature control, as feathers are thermally sensitive.
4. Role in Product Demonstration
Q: Could you describe the specific role of CIDETEC in the demonstration and manufacturing phase?
A: CIDETEC is the leader of the development phase. Our main role, in addition to the coordination of the project as a whole, is to develop the compounds with feathers. In this sense, CIDETEC builds on its previous knowledge and experience gained in the KARMA2020 project, which has been one of the main pillars of UNLOCK.
5. Scaling Challenges
Q: How do you handle the transition from small-scale batches to demo-scale production? What challenges have you encountered in scaling up the production of keratin-based bioplastics, and how have these been addressed?
A: The transition from lab and pilot scales to demonstration scale is going smoothly. The scale-up of the compounds developed in UNLOCK is being conducted by BIOMI. To do so, it is using the knowledge in feather incorporation of CIDETEC combined with their own knowledge in biopolymers processing. One of the critical aspects to be addressed in the scale-up has been the availability of treated feather, but now, after the production of treated feather at demonstration scale in the biorefinery demo plant, this hurdle has been overcome and a large quantity of treated feather is available to produce the compounds.
6. Testing
Q: What steps are taken to validate and test the bioplastics developed for agricultural use?
A: Two types of validation are being carried out at UNLOCK, on the one hand laboratory validation of the different EoLs (end of life) planned for each material (i.e. testing of biodegradation in different environments: in composting conditions, in soil) and on the other hand, validation of the products in field. In the latter case, the aim is to assess the validity of the products developed in terms of their suitability for application (whether crops grow in the same way, whether yields are the same, etc.).
7. Development of Agricultural Products
Q: Can you explain the agricultural products that UNLOCK is developing and for what use these products are applied in agriculture? What unique benefits do these products offer?
A: As mentioned above, UNLOCK is addressing 4 use cases: seed trays, mulch films, nonwoven geotextiles and hydroponic foams. Seed trays are used for growing seeds in order to obtain small seedlings of the crop that will later be planted. In the case of mulch films and nonwoven films, the purpose is to protect the crops to prevent weeds from growing, to maintain humidity, etc. Finally, foams are used as a substrate for hydroponic crops (without the need for soil). The bioplastics developed in UNLOCK offer multiple benefits in comparison to other bioplastics available in the market: faster biodegradation rate, adapted to the crops duration and EoL (end of life) and input of Nitrogen to soil at the end of they lifespan.
This project has received funding from the Bio-based Industries Joint Undertaking under the European Union’s Horizon 2020 research and innovation programme under grant agreement Nº 101023306.
This site is licensed under Creative Commons
Attribution-NonCommercial-ShareAlike 4.0 International (CC BY-NC-SA 4.0).
Website designed and coded by Fastlane